Rayon
Rayon is a manufactured regenerated cellulosic fiber.
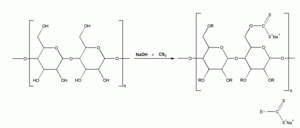
Cellulose is treated with alkali and carbon disulfide to yield viscose.
History
Rayon is produced from naturally occurring polmers and therefore it is not a synthetic fiber, but a manufactured regenerated cellulosic fiber.
Georges Audemars developed the first "artificial silk" about 1855, but his method was impractical for commercial use. Hilaire de Charbonnet, Comte de Chardonnay, patented "Chardonnay silk" in 1884, but it was so inflammable it had no safe use. Finally, in 1894, Charles Frederick Cross, Edward John Bevan, and Clayton Beadle patented the first safe and practical artificial silk, which they named "viscose." Avtex Fibers Incorporated began selling their formulation in 1910 in the United States. The name "rayon" was adopted in 1924, with "viscose" being used for the viscous organic liquid used to make both rayon and cellophane. In Europe, though, the fabric itself became known as "viscose," which has been ruled an acceptable alternative term for rayon by the Federal Trade Commission.
Rayon was only produced as a filament fiber until the 1930s when it was discovered that broken waste rayon could be used in staple fiber. The physical properties of rayon were unchanged until the development of high-tenacity rayon in the 1940s. Further research and development led to the creation of high-wet-modulus rayon (HWM rayon) in the 1950s [1].
Major fiber properties
Rayon is a very versatile fiber and has the same comfort properties as other natural fibers and can imitate the feel and texture of silk, wool, cotton and linen. The fibers are easily dyed in a wide range of colors. Rayon fabrics are soft, smooth, cool, comfortable, and highly absorbent, but they do not insulate body heat making them ideal for use in hot and humid climates [2]. The durability and appearance retention of regular rayon are low, especially when wet; also rayon has the lowest elastic recovery of any fiber. However, HWM rayon is much stronger and exhibits higher durability and appearance retention. Recommended care for regular rayon is dry-cleaning only, HWM Rayon can also be machine washed [1].
Gallery of textures
![]() A sample of rayon from a skirt, photographed with a macro lens. | ![]() Another skirt with a different texture. | ![]() A blouse with a texture similar to the second. |
Physical structure of rayon
Regular rayon has lengthwise lines called striations and its cross-section is an indented circular shape. The cross-sections of HWM and cupra rayon are rounder. Filament Rayon yarns vary from 80 to 980 filaments per yarn and vary in size from 40 to 5000 denier. Staple fibers range from 1.5 to 15 denier and are mechanically or chemically crimped. Rayon fibers are naturally very bright, but the addition of delustering pigments cuts down on this natural brightness [1].
Production method
Regular rayon (or viscose) is the most widely produced form of rayon. This method of rayon production has been utilized since the early 1900s and it has the ability to produce either filament or staple fibers. The process is as follows:
- CELLULOSE: Production begins with processed cellulose
- IMMERSION: The cellulose is dissolved in caustic soda
- PRESSING: The solution is then pressed between rollers to remove excess liquid
- WHITE CRUMB: The pressed sheets are crumbled or shredded to produce what is known as "white crumb"
- AGING: The "white crumb" aged through exposure to oxygen
- XANTHATION: The aged "white crumb" is mixed with carbon disulfide in a process known as Xanthation
- YELLOW CRUMB: Xanthation changes the chemical makeup of the cellulose mixture and the resulting product is now called "yellow crumb"
- VISCOSE: The "yellow crumb" is dissolved in a caustic solution to form viscose
- RIPENING: The viscose is set to stand for a period of time, allowing it to ripen
- FILTERING: After ripening, the viscose is filtered to remove any undissolved particles
- DEGASSING: Any bubbles of air are pressed from the viscose in a degassing process
- EXTRUDING: The viscose solution is extruded through a spinneret, which resembles a shower head with many small holes
- ACID BATH: As the viscose exits the spinneret, it lands in a bath of sulfuric acid resulting in the formation of rayon filaments
- DRAWING: The rayon filaments are stretched, known as drawing, to straighten out the fibers
- WASHING: The fibers are then washed to remove any residual chemicals
- CUTTING: If filament fibers are desired the process ends here. The filaments are cut down when producing staple fibers [3].
High Wet Modulus rayon (HWM) is a modified version of viscose that has a greater strength when wet. It also has the ability to be mercerized like cotton. HWM rayons are also known as "polynosic" or can be identified by the trade name MODAL [4].
High Tenacity rayon is another modified version of viscose that has almost twice the strength of HWM. This type of rayon is typically used for industrial purposes such as tire cord [4].
Cupramonium rayon has properties similar to viscose but during production, the cellulose is combined with copper and ammonia (Schweizer's reagent). Due to the environmental effects of this production method, cupramonium rayon is no longer produced in the United States [4].